Welcome to Part 2 of our Q&A with Russell Churchill on common issues and how to avoid them! This time, we are covering Commercial Ironers and Dishwashers – to read Part 1, on Commercial Washing Machines and Tumble Dryers, please click here.
What are the 3 most common issues you see with Commercial Ironers?
There can be a number of issues which mean we are called out to the Ironer, 3 of the most common are:
- The ironer not heating fully – this can be due to either element failures or safety stat failures.
- Poor ironing results – with an uneven wear on the roller, which can be caused by using the middle of the roller only.
- Damage to clothes and sheets – caused by a dirty or damaged ironing plate.


What are the best ways to avoid these issues?
Commercial ironers come in many sizes, and good quality machines help you process large volumes with great results. There are many other benefits as well, including saving time and money, being easy to use, and having important safety features built in. Whilst the issues mentioned above can arise, some simple steps can avoid many of these. Here’s 3 actions I would recommend:
- Ensuring the ironer isn’t left running when not in use. If it is left running, this can lead to overheating.
- Training of users, for example on using the whole roller from left to right, rather than just the middle, which helps ensure the padding is not worn unevenly.
- Advising and training users that the shoe should be cleaned and waxed at a set timeframe to prevent any marks on the ironing plate causing damage to the fabrics being ironed. For further assistance with this , please see a guidance video we have produced to help with this – JTM Service – How To Wax And Clean Your Ironer
What are the 3 most common issues you see with Commercial Dishwashers?
Dishwashers can be hood-type or undercounter, and can be freshwater or tank. Each type of dishwasher has their own potential issues, but 3 of the most common issues we come across are:
- The dishwasher being clogged up and giving poor results – this is often due to debris not being scraped off the items before being loaded. Large pieces of food should be removed before loading.
- Leaking from the dishwasher – this can be from component failures, or possible damage caused by the user overloading or misusing the machine.
- Poor wash result – using the wrong detergents, dosing incorrectly, or not using salt can mean poor results. It will also damage the machine.
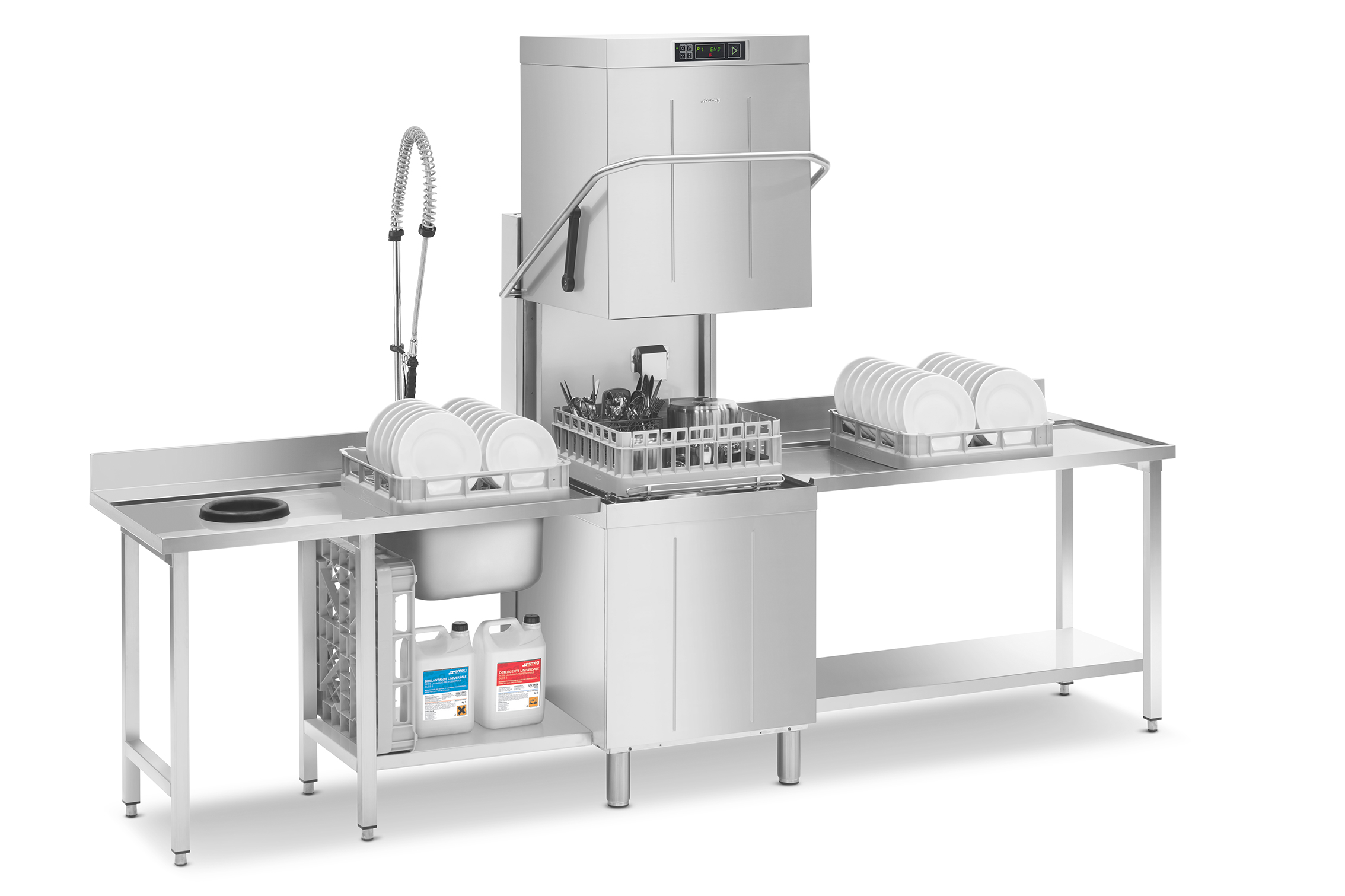
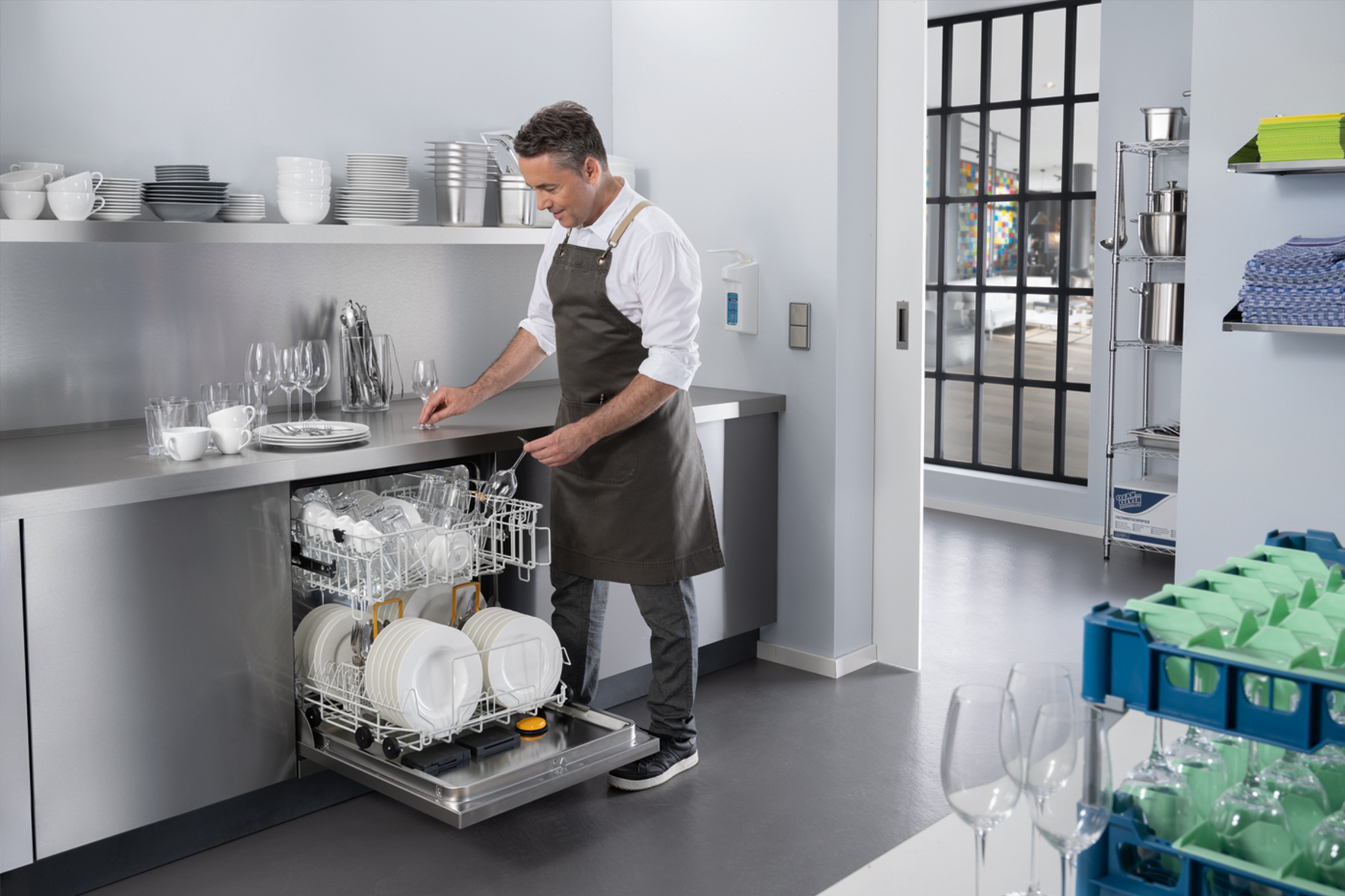
What are the best ways to avoid these issues?
Many of the common issues can be avoided. Here are some actions which should be taken to help:
- Training the team on the correct usage of the machine, including removing large food items before loading, and the importance of salt to improve wash performance and prevent limescale build up, will help give the best results and reduces breakdowns.
- Routine preventative maintenance visits to identify any issues before they affect the running of the machine, and to ensure it is running efficiently and effectively.
- Using the right, specialist commercial detergents; making sure the dishwasher is dosing correctly; and keeping the water softener full of salt.
Russell Churchill is our Head Technical Engineer at JTM Service. He has worked as an Engineer in the industry for over 25 years, and being with JTM Service for 16 years. You can find more details about Russell, including his role at JTM Service, and his even more important role as “Dad’s Taxi”, here –https://jtmservice.co.uk/meet-the-team-russell-churchill/!
If you would like to discuss anything raised in this Q&A, or understand how JTM Service can support you, please contact us on 0113 2572221 or email service@jtmservice.co.uk.