For the next in our series of Q&As with Russell Churchill, our Head Technical Engineer here at JTM Service, we asked him to tell us about some of the common issues he sees and his advice on how to avoid them.
In part 1 we cover Commercial Washing Machines and Tumble Dryers, and we’ll cover Ironers and Dishwashers in part 2 separately.
What are the 3 most common issues you see with Commercial Washing Machines?
There can be a number of issues which mean we are called out to the washing machine, 3 of the most common are:
- Failure of a single component on a machine stopping it functioning to the best of its ability, such as blockages in drain pumps or filters, heater element failures or even failed electronic boards
- Poor washing results – incorrectly loaded machines will not fully clean the washing, with some deposits still being present at the end of the cycle, which will mean rewashing, which is both not energy efficient and also unhygienic
- Damage to the machine caused by incorrect use of chemicals, such as damaged hoses and seals from using chemicals designed for low temperature washes at higher temperatures
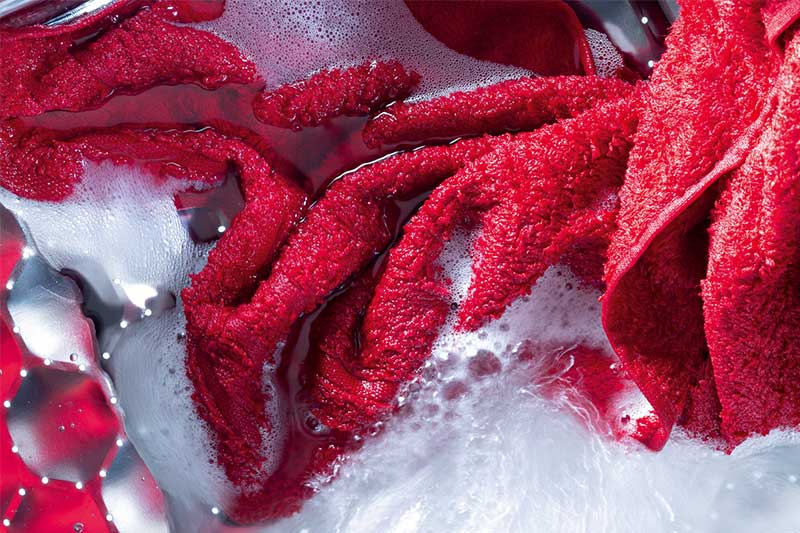

What are the best ways to avoid these issues?
Good quality commercial washing machines are robust, efficient and give great cleaning results. Whilst the issues mentioned above can arise, some simple steps can avoid many of these. Here’s 3 actions I would recommend:
- Getting the machine regularly serviced to ensure the machine is operating efficiently and effectively, and to highlight any possible impending failures before they happen
- Training of users, for example regarding load size
- Advising all users about the correct use of the chemicals that are needed for washing, including which chemicals are designed for low temperature washes
What are the 3 most common issues you see with Commercial Tumble Dryers?
3 of the most common issues we come across are:
- Safety systems built into the machine cutting in, which prevents the dryer from operating to avoid further damage
- Overloading, which causes poor airflow and possible component failures
- Excessive lint build up in the machine and in the ducting, reducing efficiency and effectiveness, and causing a fire risk
What are the best ways to avoid these issues?
Again, there are some actions which should be taken to avoid many of these issues:
- “Airflow is King” with tumble dryers, and regular servicing by a specialist company will check all these safety systems are protecting the machine and not triggering unnecessarily
- Advising and training users about load size and the dangers of poor onsite maintenance
- Cleaning the filters at the absolute minimum every day, more realistically every few cycles and getting the tumble dryer regularly serviced and the ducting cleaned. This should be at least every 12 months, or more often as required. Also ensure the Annual Gas Safety Inspection is done by a registered Gas Safe engineer to keep up to the legal requirements
Thank you to Russell for this Q&A, and please look out for part 2 on Ironers and Dishwashers soon! And if you would like to discuss anything raised in this Q&A, or understand how JTM Service can support you, please contact us on 0113 2572221 or email service@jtmservice.co.uk.