Contaminated laundry is one of the main ways harmful bacteria can spread leading to an outbreak of infections, and it is essential to manage this risk in settings such as Healthcare, Care and Hospitality.
Effective hygiene and infection control processes and practices in a commercial on-premise laundry help to protect you, your team and your customers. But what are the best ways to maximise infection control?
- Personal hygiene – maintain strong hygiene precautions, such as providing handwashing facilities and alcohol gels and requiring stringent use. 80% of common infections are spread by hands!
- PPE – wear appropriate Personal Protective Equipment (PPE), such as masks, disposable aprons and gloves.
- Staff training – turnover of staff in laundries can be a major issue, so employees should be thoroughly briefed and trained, and this should be repeated regularly.
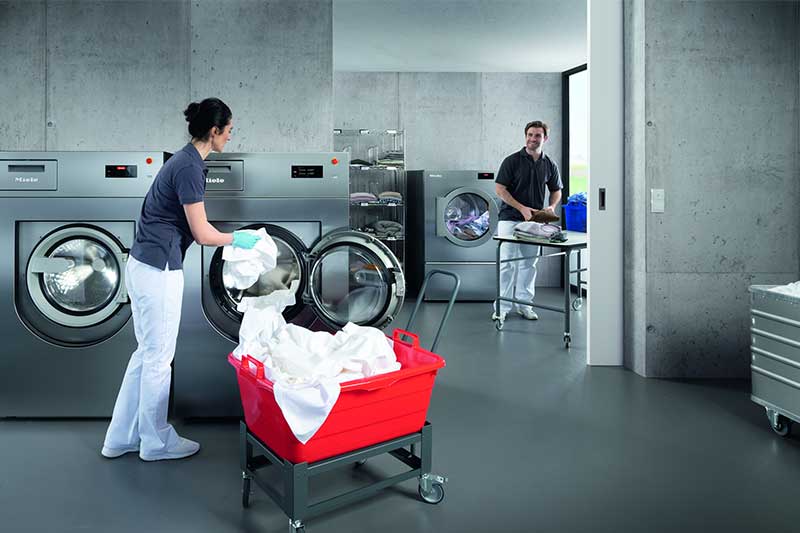
4. Process and Procedures – it is essential to have clear written laundry procedures in place and that these are managed and followed.
5. Storage of Linen – prior to washing, all linen and garments should be stored in a secured area.
6. Handling contaminated linen – movement of linens should be minimised prior to washing to avoid contaminants being spread into the air and onto nearby surfaces.
7. Separate laundry and avoid cross contamination – good practice is required at every stage of the linens laundry journey, ensuring soiled linen is collected, stored and transported separately from clean linen and correct methods are used such as designated containers and red water-soluble bags.
8. Correct Equipment/Machines – using WRAS approved commercial laundry equipment which is fit for the purpose it is being used, such as washing machines with a gravity drain, and with thermal disinfection programmes.
9. Correct programmes are used – users often do not select the correct temperature programs, using lower temperature non-thermal disinfection cycles. Department of Health Guidance in HTM 01-04 states the disinfection cycle should maintain 65°C for at least 10 minutes or 71°C for at least 3 minutes. Use of lower temperatures also may not dissolve red bags.
10. Equipment is maintained and serviced – if equipment is faulty or poorly maintained the effectiveness of the wash may be affected and equipment downtime may impact the ability to launder all the linen required.
11. Daily Clean-down – a structured daily wipe down of all surfaces, such as door handles and control screens and buttons.
12. Temperature validation – perform regular validations to ensure the correct time-temperature relationships are being met to meet recognised disinfection standards such as the NHS infection control guidelines for health and social care (HTM 01-04).
At JTM Service we have over 35 years’ experience providing support to businesses including Care Homes, Hospitals, Housing, Animal Care and Hotels and Hospitality. If you have found these 12 Tips useful and would like more information on the prevention of infection in your on-premise laundry please get in touch at info@jtmservice.co.uk or call 0113 2572221.
Find out more at https://jtmservice.co.uk/ #proudtobejtmservice #care #commerciallaundry #littlegiants #commercial #laundry #washing #machines #commercial #dishwashers
Download a pdf showing the 12 Tips For Infection Control in a visual format.